Beyond Reduce, Reuse, Recycle: Calyx’s Holistic Approach to Sustainability | Calyx Containers
We're taking a wider lens on sustainability and unveiling the environmental impact of Dram and Concentrate packaging. Discover how our mindful product design and manufacturing paired with a domestic-first supply chain contribute to superior sustainability performance when compared to the competition.
Beyond Reduce, Reuse, Recycle: Calyx’s Holistic Approach to Sustainability | Calyx Containers
Stay in touch!
Join our email list to receive Calyx content & product updates.
By Nicole Erickson in Cannabis Packaging
Quick Hits
- Calyx conducted comprehensive Life Cycle Analyses spanning manufacturing to delivery to shed light on the environmental footprint of two flagship products versus competitive packaging.
- The Calyx 25 Dram Container showcases up to a 32% reduction in emissions compared to similarly sized competitive products.
- The Calyx 7mL Concentrate exhibits up to a 46% decrease in emissions compared to competitive concentrate packaging.
- We achieve these striking reductions in emissions through our predominantly domestic supply chain and innovative Bi-Injection Molding manufacturing process.
Elevating Sustainability Standards
Each Calyx product is mindfully made with the three Rs—Reduce, Reuse, Recycle—at the core of our design and manufacturing process. While these principles lay a strong foundation for sustainability, we believe their true impact is realized within a broader context. That's why we take a multi-dimensional approach, analyzing the life cycle of our products from design to distribution and ensuring that every step aligns with our commitment to sustainability.
But we don't stop there. We go the extra mile by conducting competitive analyses to see how our products compare in the marketplace. Why? Because we genuinely care about helping you meet your sustainability goals. By understanding where we sit in the market, we can identify areas for improvement and innovation to be confident that our products not only meet, but exceed your expectations when it comes to sustainability.
Going Beyond the Basics with Life Cycle Analysis
Each product in the marketplace has gone through a multi-step journey to get into your hands. That journey accumulates a variety of financial costs from manufacturing to shipping, as well as environmental costs. These environmental costs are quantified by a different set of standards.
LCA, or Life Cycle Assessment, is a powerful tool used to evaluate the environmental impact of a product, process, or activity throughout its entire life cycle. It can encompass a diverse range of steps, from raw material extraction to production, distribution, use, and disposal. However, it's essential to recognize that every LCA necessitates the identification of these steps, as well as making thoughtful assumptions, to ensure an accurate portrayal of a product’s environmental footprint.
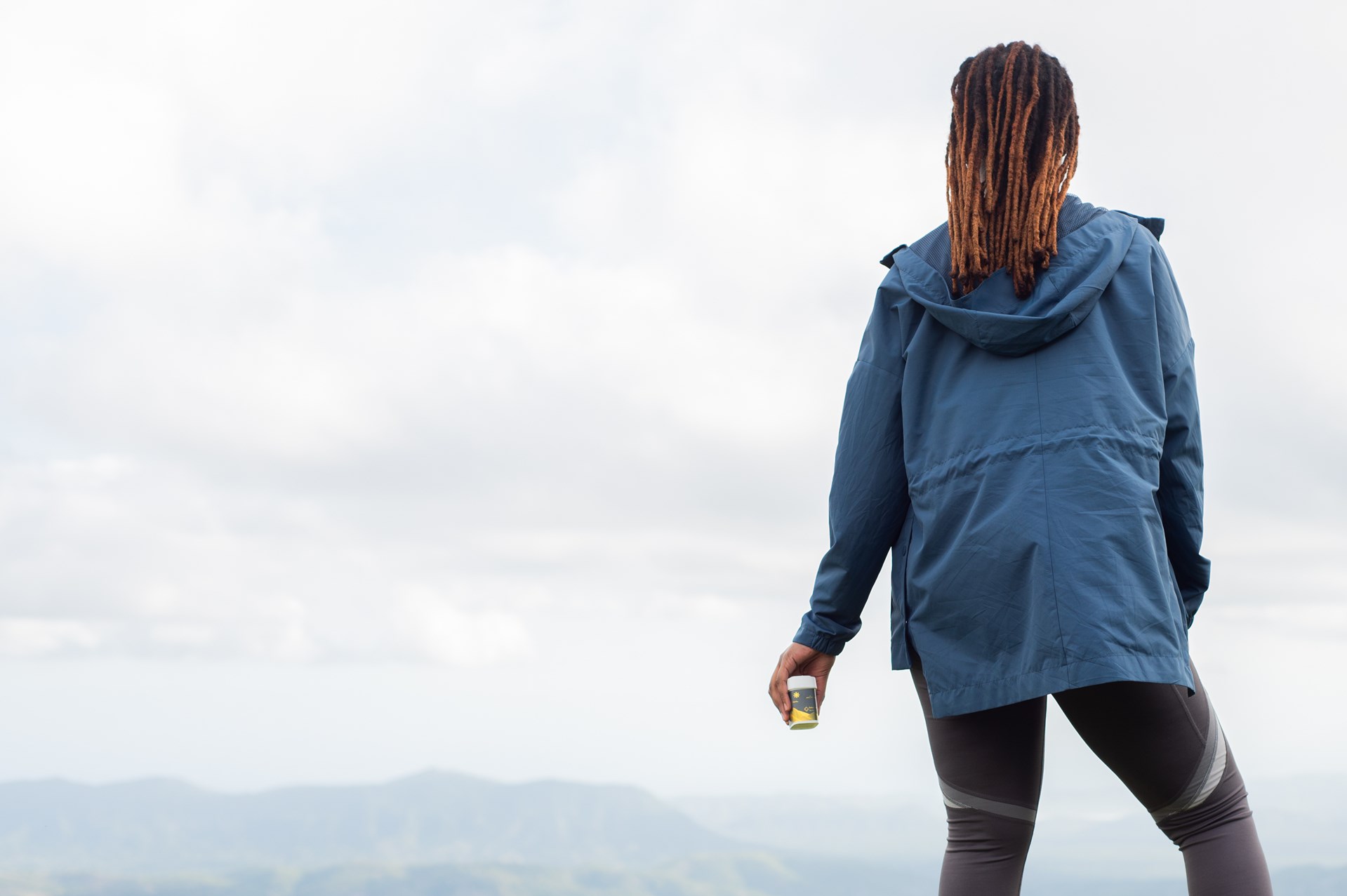
To ensure accuracy, our analyses focus on steps within our control, minimizing assumptions and providing a more precise view of our products' environmental impact. Unlike simple shipping cost evaluations, our LCAs delve into every facet of our products’ journey from manufacturing to transportation and delivery to our customers.
Quantifying Life Cycle Impact in CO₂eq
CO₂eq, or carbon dioxide equivalent, serves as a standardized unit of measurement used across industries to gauge environmental impact through multiple lenses including human toxicity, ozone layer depletion, and Global Warming Potential (GWP). This standardization allows for direct comparisons between different activities, processes, and products, even when they emit pollutants with different lifespans and potencies.
CO₂eq is determined by multiplying the mass of a non-CO₂ climate pollutant by its Global Warming Potential. GWP values vary depending on the time horizon considered, as a product's impact can differ over various timescales. We utilize the CO₂eq measurement specifically to illustrate the product's impact on Global Warming Potential averaged over 100 years (GWP100a).
- A higher CO₂eq signifies greater harm to our planet.
- We aim for the lowest possible emissions of CO₂eq and benchmark against competitive packaging to ensure our efforts are on the forefront of building a more sustainable cannabis industry.
CO₂eq serves as a standardized unit of measurement to gauge environmental impact. It allows for direct comparisons between different activities, processes, and products, even when they emit pollutants with different lifespans and potencies.
Calyx Products Have a Gentler Impact on Our Planet
Let’s dive into the data and take a look at two sets of Life Cycle Analyses comparing our Dram and Concentrate Containers versus the competition.
Calyx Drams Set New Sustainability Standards
In conducting this Life Cycle Analysis, we meticulously traced the journey of a 25 Dram Container from manufacturing to its final delivery destination in a central US state and one of the most mature cannabis markets, Colorado. Our focus was on comparing the environmental impact of our 25 Dram Container against two alternative containers of similar size, revealing a clear superiority over our competitors in emission reductions.
The CO₂eq emissions for a single Calyx 25 Dram container stand at a mere 0.17 kg, underscoring its minimized environmental footprint when compared to alternative options. In contrast, an 1/8th Palm + Turn Container emits 0.25 kg, while a 30 Dram Pop Top container releases 0.24 kg of CO₂eq, highlighting the significant advantage of our product in terms of environmental impact.
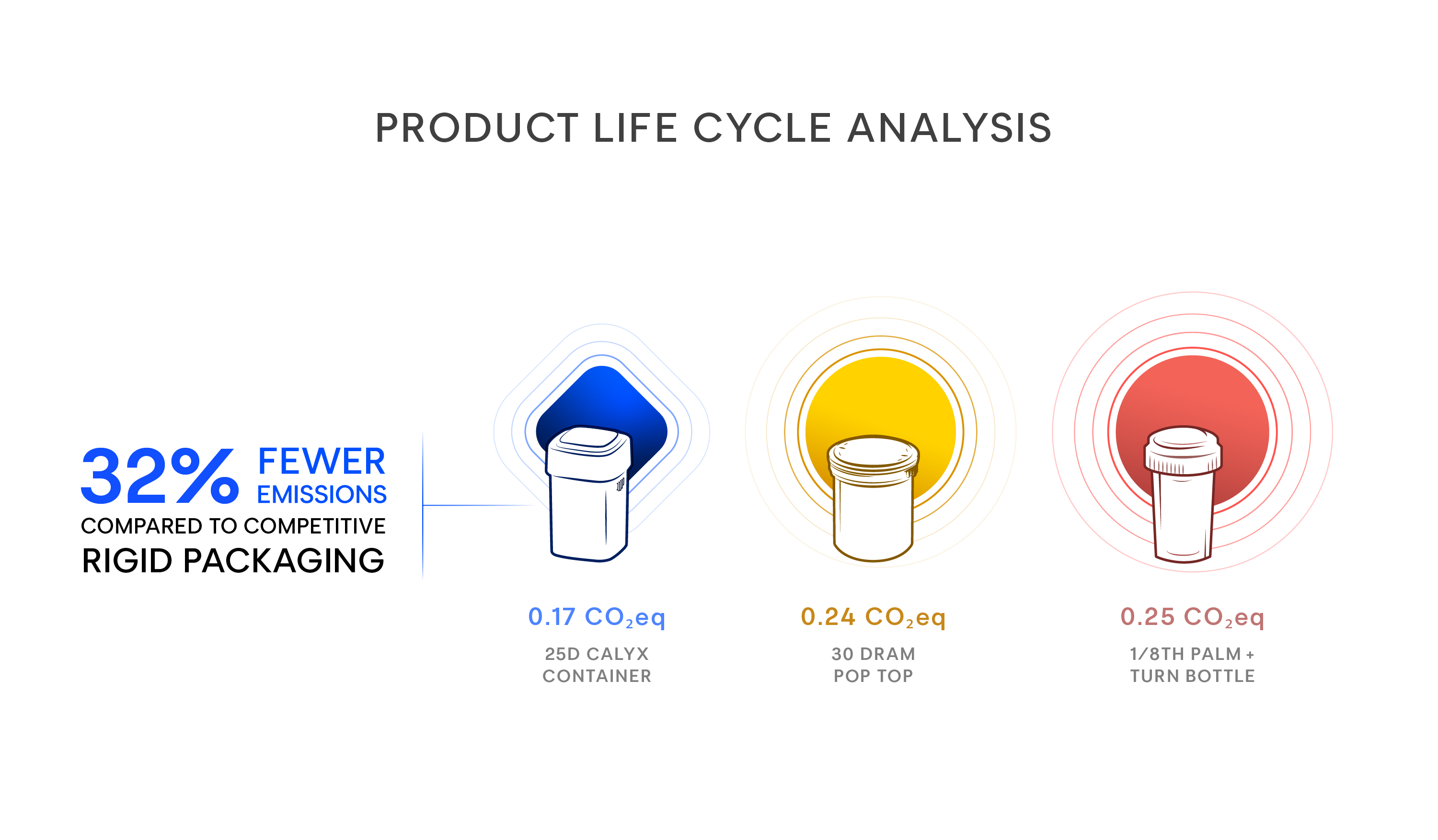
Making an Impact at Scale
To put these results in perspective, consider this: for every two competitive containers—whether 1/8th Palm + Turn or 30 Dram Pop Top—you could produce three Calyx 25 Drams and have the same environmental impact!
Let’s zoom out a bit further. If you were to purchase 100,000 Calyx 25 Drams, you would only be able to purchase 66,700 competitive packages while emitting the same value of CO₂eqs.
Now, let's look through an even wider lens. Your business operates at scale, with long-term goals and sustainability commitments. Imagine the cumulative impact on your annual packaging emissions over a period of five years, or even a decade. By opting for a product consciously crafted for sustainability, you're not just making a short-term decision—you're shaping the environmental footprint of your business for years to come and leaving a legacy of responsible stewardship for future generations.
For every two competitive containers—whether 1/8th Palm + Turn or 30 Dram Pop Top—you could produce three Calyx 25 Drams and have the same environmental impact!
What Makes Calyx Drams Different?
Domestic Supply Chain
The key distinction between Calyx Drams and competitive rigid cannabis packaging lies in their manufacturing locations. Calyx Drams are proudly made right here in the USA, while competitors rely on offshoring their manufacturing activities to China. The geographic variance between manufacturing and delivery locations leads to significantly longer shipping distances and vastly different amounts of energy being used for transportation and delivery.
Product Design
Product design is another key factor driving Drams’ lower CO₂eq. Our zero waste bi-injection lid manufacturing process involves molding two distinct plastics into a single lid—encasing the soft thermoplastic gasket material within the hard polypropylene shell in one efficient operation. By consolidating production into a singular process, we minimize waste, streamline production time, and reduce energy consumption.
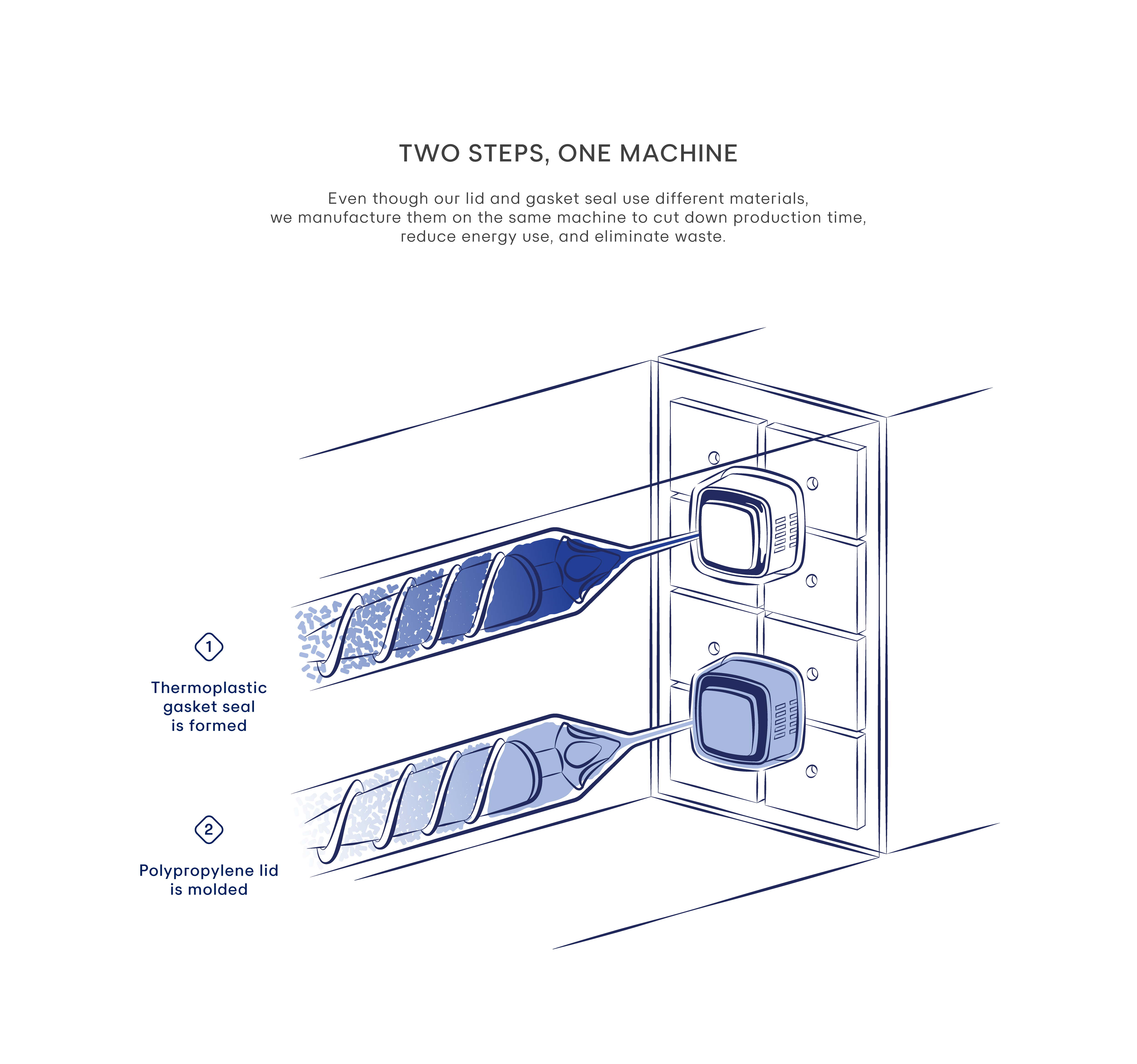
Calyx Concentrate Containers Lead the Pack
Much like our Dram containers, the 7mL Unlined Calyx Concentrate Container outperformed competitive extract packaging. The Calyx 7mL Concentrate emits just 0.13 kg of CO₂eq per package, compared to the 7mL competitive package at 0.24 kgs of CO₂eq. That’s a mind-blowing 45% decrease in emissions!
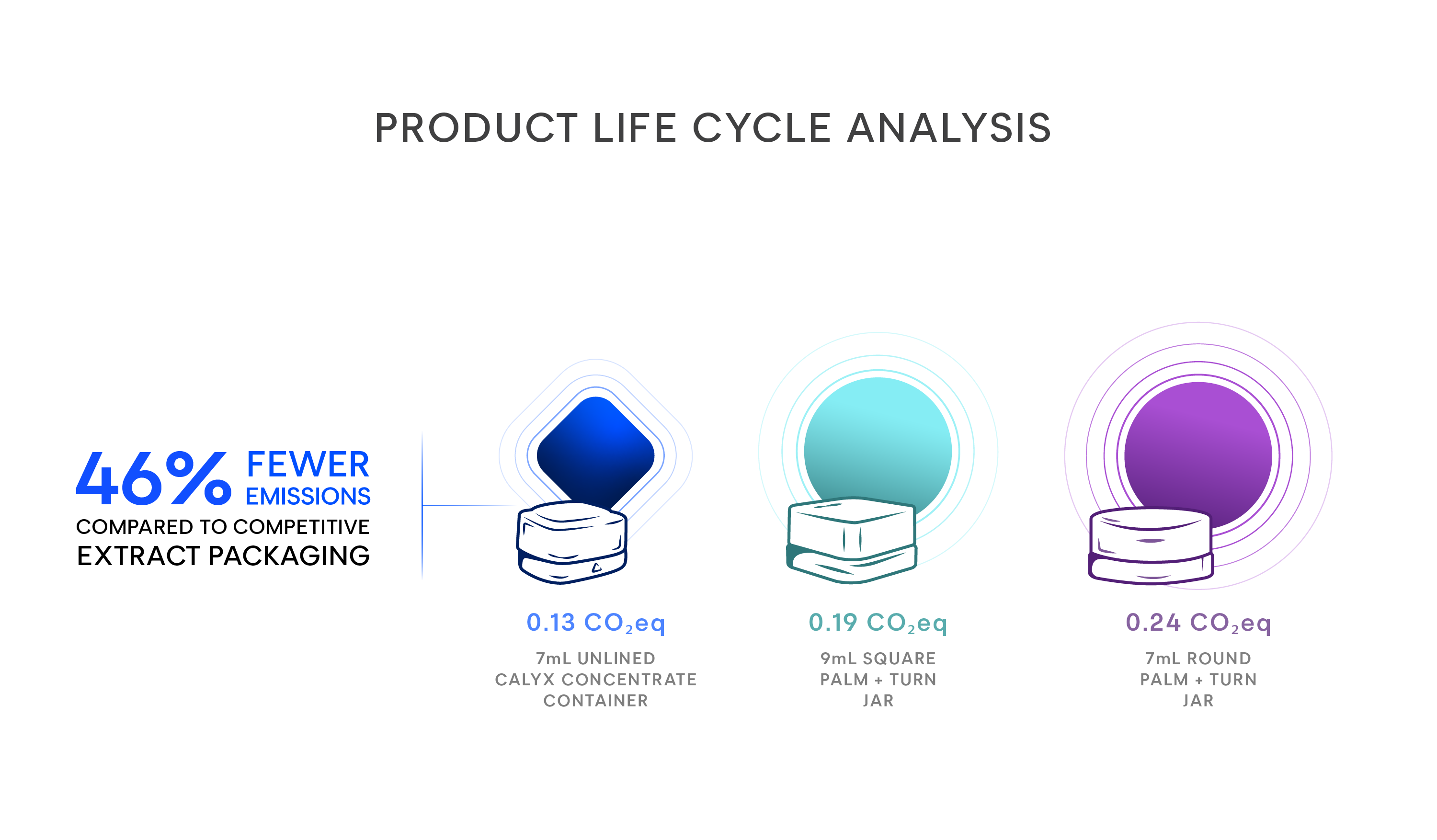
Our Calyx Concentrate LCA follows a similar trajectory to our Drams, beginning with manufacturing and ending with distribution to Colorado. However, it diverges from the Dram analysis with one crucial distinction: both Calyx and competitors’ glass bases are sourced internationally, necessitating overseas transportation to reach their final distribution points. Continue reading to learn why our glass is manufactured outside US borders and how our Concentrates still achieves a lower GWP (CO₂eq) compared to rival products.
What Makes Calyx Concentrates Different?
Strategic, Sustainable Partnerships
We pride ourselves in our US based supply chain and produce domestically whenever possible. However, we choose to produce our glass internationally in order to balance our core values of quality and sustainability. We strategically partnered with a European glass manufacturing expert in order to leverage their deep knowledge and strong quality focus, in addition to other factors that make us confident in the partnership:
- Robust Recycling Infrastructure and Circular Economy Impact: We capitalize on Europe's advanced glass recycling infrastructure to integrate Post-Industrial Recycled (PIR) content into our glass Calyx products so we can contribute to a circular economy on an industrial scale. Glass recycling is only economically viable within efficient collection systems that separate out like materials and even colors, and Europe has mastered efficient collection systems at the industrial and consumer levels. In contrast, the US still uses single stream recycling systems that require less cost, infrastructure, and consumer education to implement versus multi-stream systems, but yield inferior results.
- Sustainable Operations: Our manufacturing ally has earned a Silver Medal from Ecovadis, an organization known for its reputable and reliable assessments of enterprise level sustainability practices. This assessment reinforces our confidence that our values and operational ethos are in alignment.
- Renewable Energy: With a steadfast dedication to sustainability, our partner exclusively employs 100% renewable energy sources, underscoring their commitment to environmental stewardship.
Our partner’s impressive sustainability credentials factored in our decision to manufacture glass overseas, and we pass these environmental efficiencies along to your brands when you choose Calyx and reduce the environmental impact of your extract packaging. We take pride in this partnership, knowing that it’s the right choice to deliver the high quality and environmentally conscious glass your customers know and love.
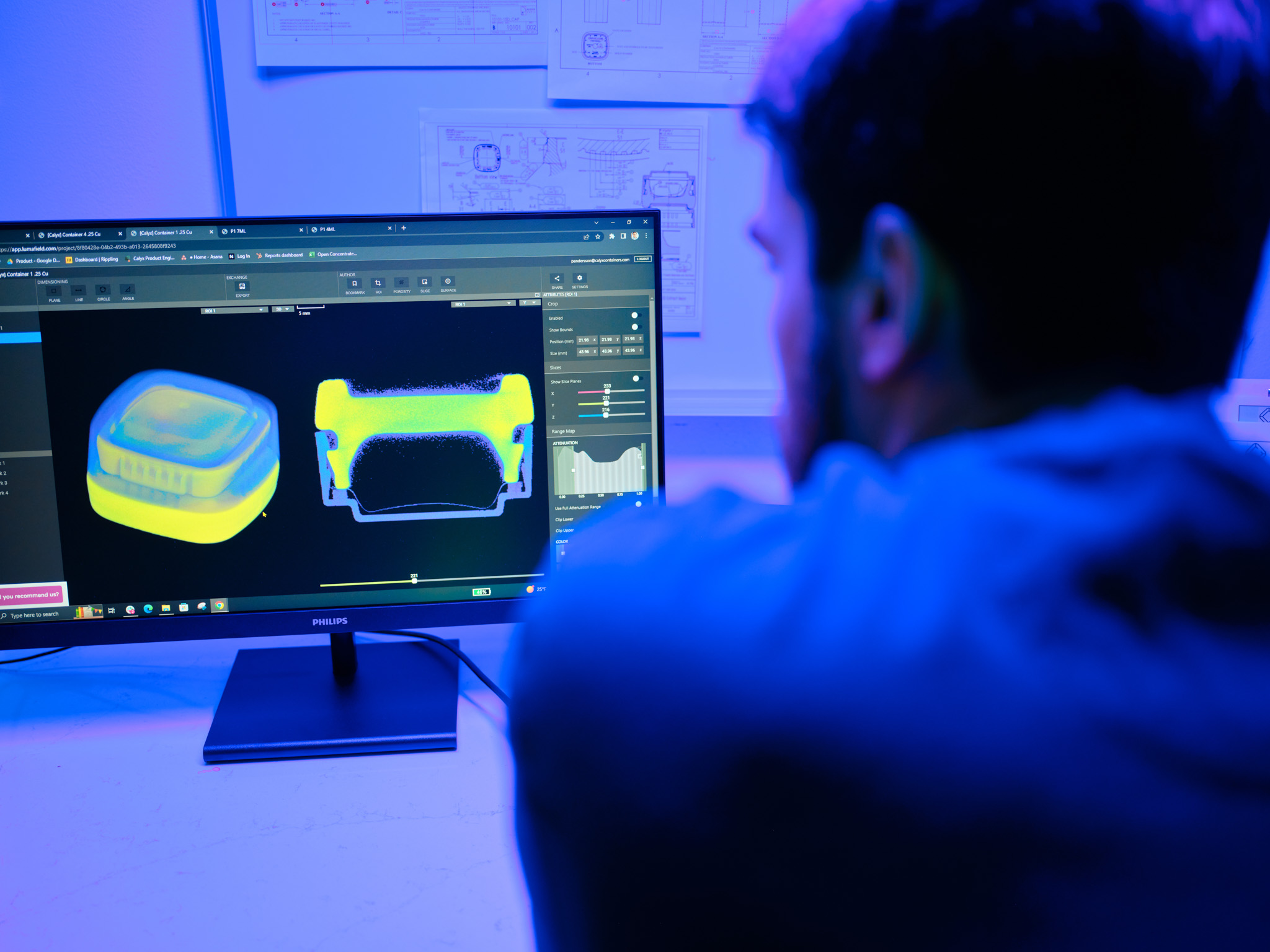
Environmentally Conscious Design
Calyx Concentrate Lids are mindfully designed for manufacturing via a Bi-Injection Molding process. This zero waste process significantly contributes to Calyx Concentrates’ superior performance along sustainability metrics, just like our Dram Containers.
In contrast, competitive concentrate lids typically undergo a two-step production process: first, injection molding, followed by a secondary liner manufacturing and insertion process. Not only do competitive lids involve two separate production processes, but they also utilize two distinct materials for the lid versus the liner, leading to a higher CO₂eq footprint. Additionally, the presence of the liner complicates recycling efforts for consumers, who need to be educated and motivated to remove the liner before recycling. That’s a detrimental double blow to our environment.
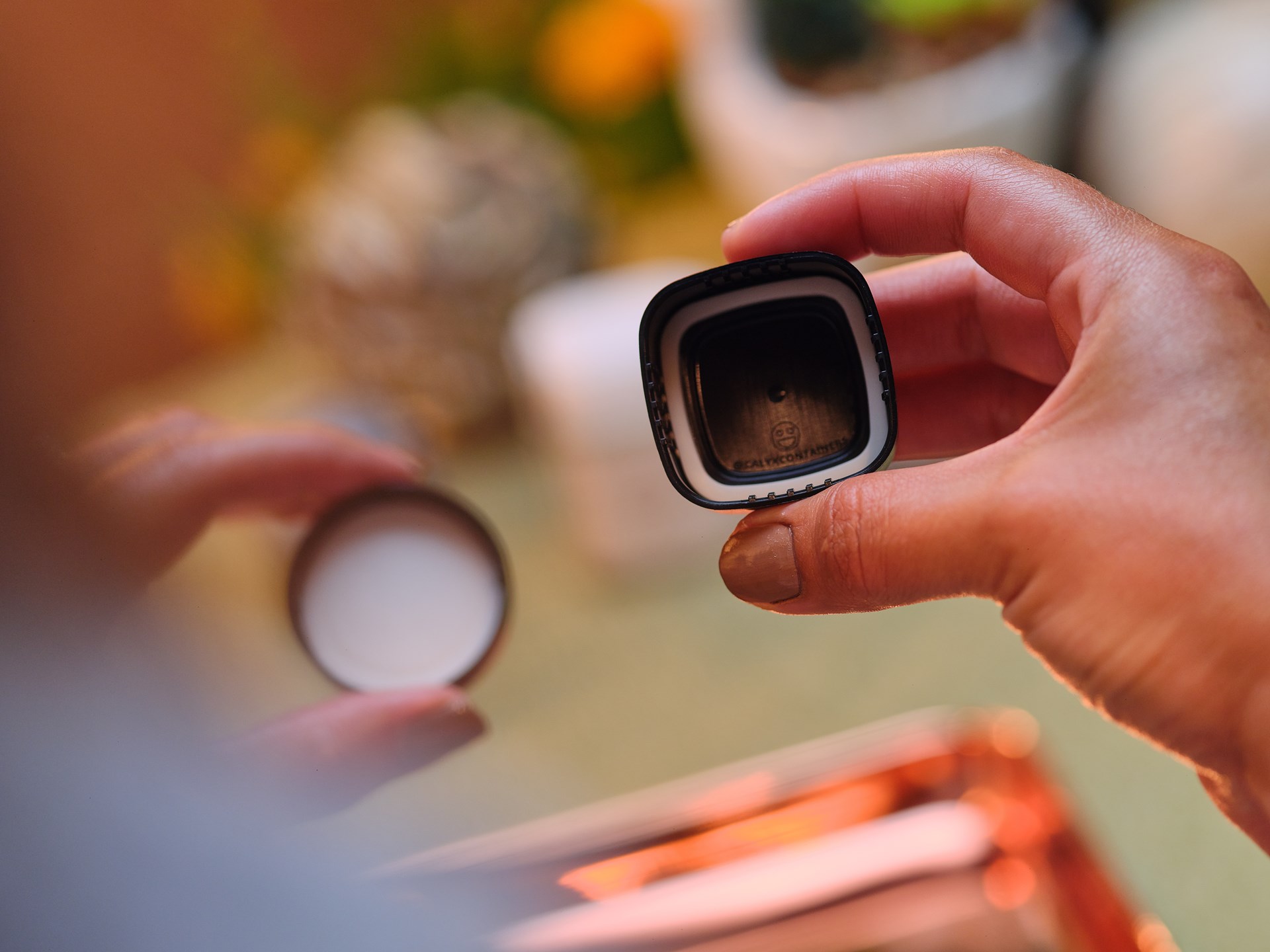
Calyx also uses two separate materials for lids and our secondary gasket seal, but due to the materials’ similarity they can be recycled without disassembly. That’s one less thing for consumers to consider at the product’s end of life, leading to a higher chance of recyclability.
Not only do competitive lids involve two separate production processes, but they also utilize two distinct materials for the lid versus the liner, leading to a higher CO₂eq footprint than Calyx Concentrates.
Sustainability Is Multi-Dimensional
At Calyx, we’re focused on more than the three Rs. We value these tangible sustainable practices while employing a more holistic approach to truly understand our impact on this shared planet. By leveraging our US-based supply chain and reducing manufacturing waste via thoughtful product design and efficient manufacturing processes, we’re supporting our shared commitment to a sustainable future in high performance cannabis packaging.